Environmental incidents and emissions
As part of our management systems we record incidents (occurrences noted by our own staff which may or may not have led to a complaint) and complaints (arising from external sources).
The number of incidents rose from 233 to 287, reflecting greater diligence in reporting, but complaints fell to 143, the lowest level for four years and very close to our target of 137. Dust was again the most common cause of complaints but we expect to see an improvement in this area following major investments at Ribblesdale and Ketton cement works in new dust filtration systems and further investments in wheel washing and dust suppression equipment at our quarries.
Environmental management is included in our specialist IEMA training programme for managers (see employment and skills).
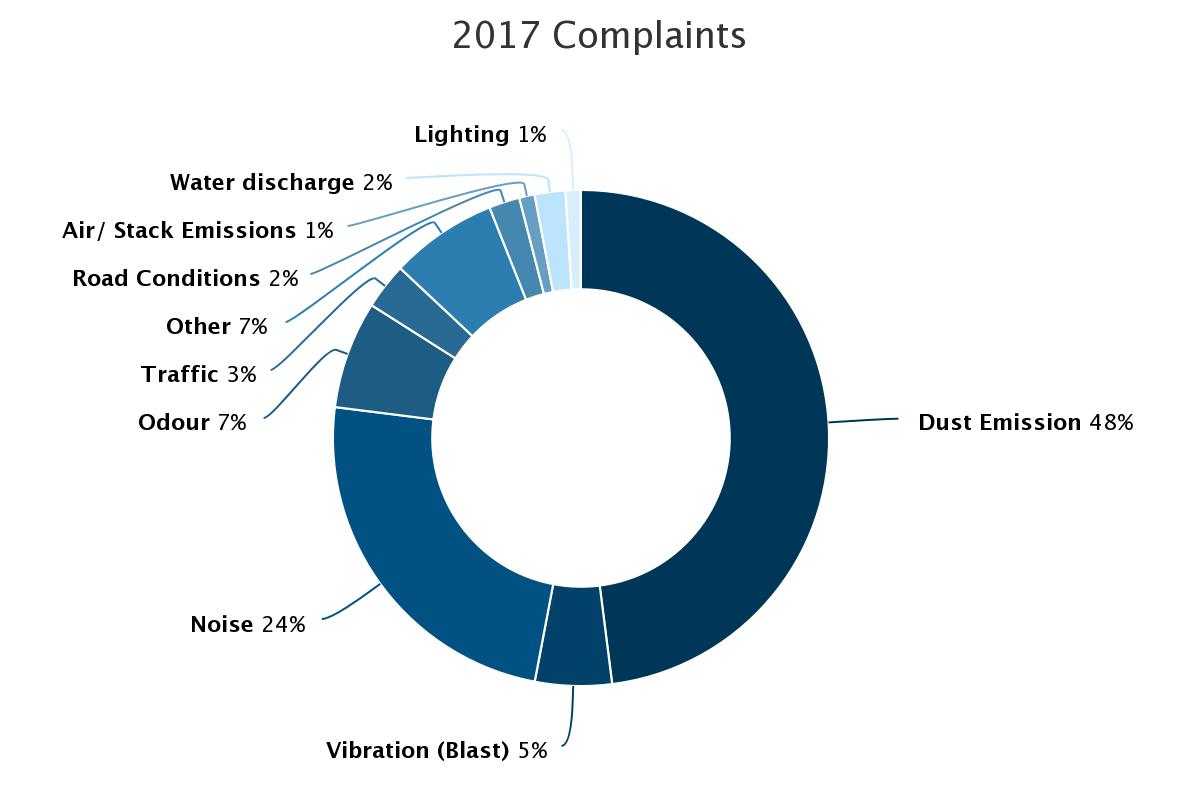
-
Incidents, complaints and prosecutions
2010 (baseline)
2015
2016
2017
Incidents
167
292
233
287
Complaints
286
191
214
143
Prosecutions
1
1
0
0
Target: 10 per cent year-on-year reduction in complaints based on 2010 figures.
Emissions from cement production
Emissions of dust, sulphur dioxide (SO2) and oxides of nitrogen (NOx) from our three cement plants remain well below the industry targets set in 2015. SO2 emissions are related to the presence of volatile sulphur compounds found in the quarried raw materials, so vary depending upon the part of the quarry that is being used.
Dust emissions from cement production fell by nine per cent in 2017 as a result of a £3 million investment in new fabric filters on the cement mills at Ketton and Ribblesdale. This keeps us below our 2020 target and further reductions are expected in 2018 with the replacement of the kiln filter at Ketton.
The implementation of the industrial emissions directive best available techniques (BAT) conclusions set a new lower NOx limit of 450 mg/Nm3 in April 2018, but there has been little change in NOx emissions as the kilns were already operating close to the new value.
There was a temporary authorised increase in SO2 emissions at Ribblesdale when the old gas scrubber was taken out of operation in August 2017. This affected the annual performance figures. A new scrubber will be commissioned in April 2018 which will reduce both SO2 and dust emissions from the kiln.
Permit breaches
The replacement of the gas scrubber at Ribblesdale led to unavoidable exceedances of the daily hydrogen chloride emission limit during raw mill maintenance periods. The potential for these breaches to occur, their negligible environmental impact and alternative control measures put in place were discussed and agreed with the Environment Agency before the project commenced.
We publish annual reports of cement plant emissions on our website at www.hanson.co.uk.
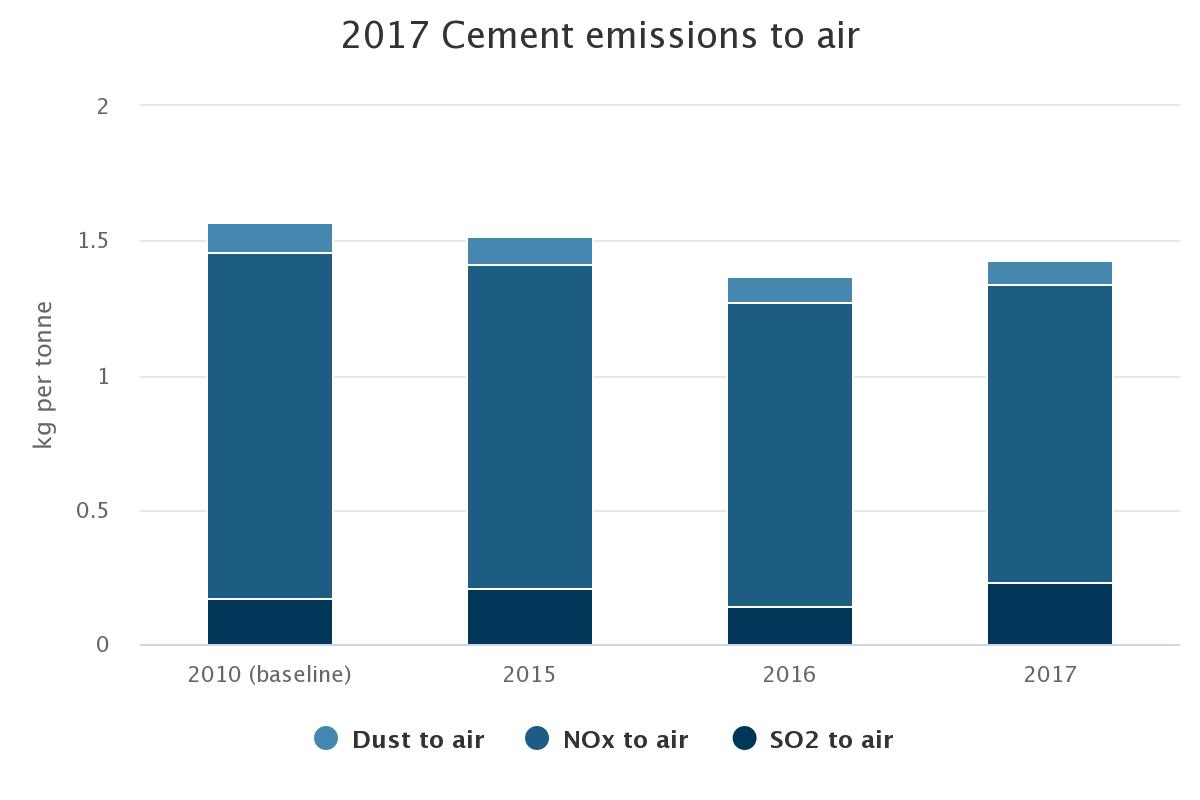
-
Cement specific emissions - kilogrammes per tonne
2010 (baseline)
2015
2016
2017
Dust to air
0.11
0.11
0.10
0.09
NOx to air
1.29
1.20
1.13
1.11
SO2 to air
0.17
0.21
0.14
0.23